Heat treatment
Metal-hardening technology in our in-house hardening facilities
Berger metal-hardening technology has been well-known worldwide since 1985, because Precision in perfection is also a vital matter for us in the field of heat treatment. With our own in-house hardening facilities at the locations in Memmingen and Poland we are a leading service provider internationally for customer-specific forms of heat treatment, and in the meantime we have become a partner for a great many leading companies including, among others, ones from the automotive sector and machine construction. We not only harden parts that we have produced ourselves, but also provide a service for other companies as a contractor.
Currently we have free capacity available.
Our expertise in metal-hardening technology
A high degree of innovation and exemplary quality make us a reliable partner – and this applies even as early as the development and project phase. The most modern and fully automatic lines are at work around the clock in our metal-hardening facilities for our customers.
Here we process case-hardened steels, tempered steels, roller bearing steel, spring steel, tool steels, non-rusting steels, aluminum alloys, etc.
Depending on the customer requirements, the batching can be done as individual items, small batches or in bulk.
Chamber furnace line
Production procedures under a conventional inert gas atmosphere with oil quenching
The chamber furnace line comprises procedures such as carburizing, single and direct hardening, quenching and tempering, as well as case-hardening and carbonitriding, various forms of tempering and annealing treatment under an inert gas and atmosphere, and deep-cooling under LN2 on the evaporation principle.
Our procedures:
- Carburizing
- Single and direct hardening
- Quenching and tempering
- Case-hardening
- Carbonitriding
- Various forms of annealing
- Tempering
- Deep-cooling
Vacuum furnace line
Production procedures with N2 high-pressure gas quenching up to 20 bar
Vacuum technology with gas quenching is characterized by low warpage and dry. clean hardening. A further advantage is that that there is almost no surface oxidation on the components. This procedure can also lead to cost reductions to the entire production chain. Process development at Berger requires this to be considered all the way through production.
Our procedures:
- Vacuum direct hardening
- Low-pressure carburizing
- Various forms of quenching and tempering
- Vacuum case-hardening
- Deep-cooling
- Gas nitriding and nitrocarburizing
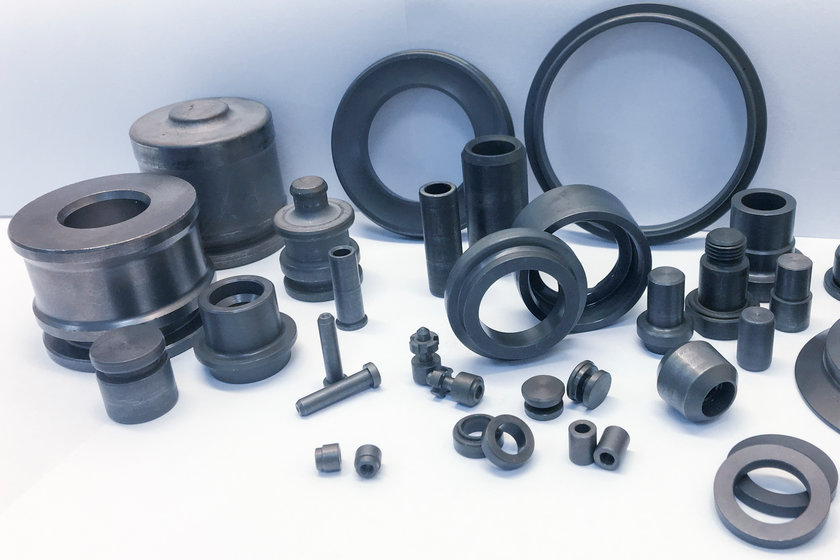
Additional procedures for heat treatment
Production procedures of the inductive units include:
- Inductive hardening
- Inductive tempering
The spectrum for heat treatment is rounded out by suitable options for component cleaning. Washing, degreasing or oiling are done in integrated cleaning systems that use hydrocarbons and/or are combined with aqueous media that are used during or after the heat treatment.
Quality assurance
In addition to conventional hardness testing we also offer microstructure investigations and evaluations, and analyses of damage. Our spectral analyzer makes it possible for our customers to determine and distinguish between the materials and their chemical composition in a definitive, reproducible way.
Hardening also includes quality assurance. After the hardening process the parts are tested using the requisite procedures according to the details given in the test plan. We carry out Vickers, Rockwell and Brinell tests. The fully automatic hardness tester can test up to six samples at the same time, with the test results being electronically recorded, documented and archived.
All the processes are carried out with due regard for the strictest current certification requirements:
- ISO 9001:2015 / IATF 16949:2016 (Quality)
- ISO 14001:2015 (Environment)
- ISO 50001:2011 (Energy)